This website uses cookies so that we can provide you with the best user experience possible. Cookie information is stored in your browser and performs functions such as recognising you when you return to our website and helping our team to understand which sections of the website you find most interesting and useful.
Tin
Non-toxic, ductile and malleable metal, strategic in the new economy
Where is it used?
In the automotive industry
In this sector, this mineral is key to the development of the electric vehicle.
Brake pads use tin additives; seat cushions use tin catalysts; bearings use a tin alloy and batteries use tin alloys.
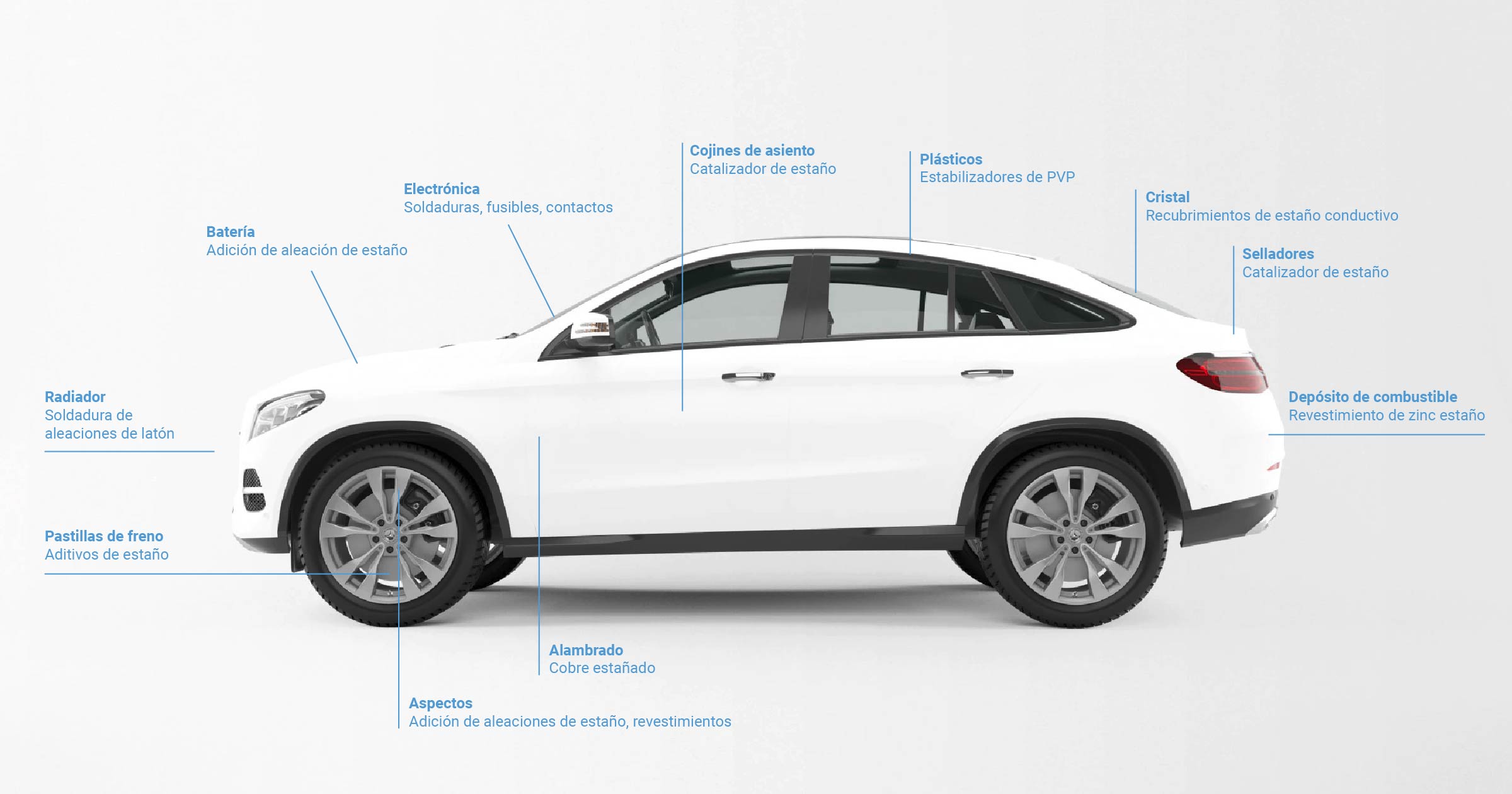
Technology
This mineral has extensive application in this sector, especially for soldering on processors, as all electronic devices contain tin to some extent.
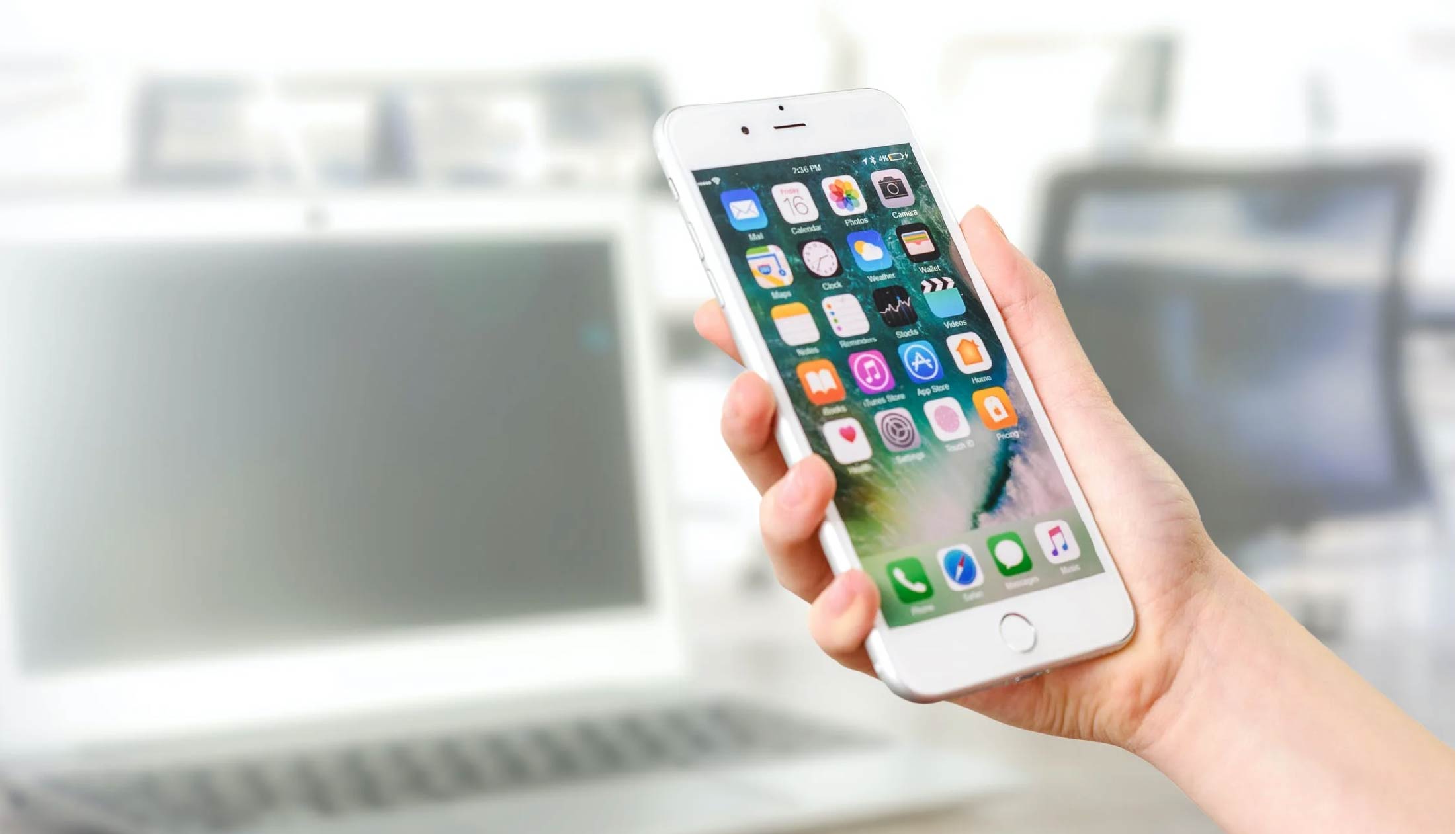
Optoelectronics
Tin oxides are electrically conductive and transparent.
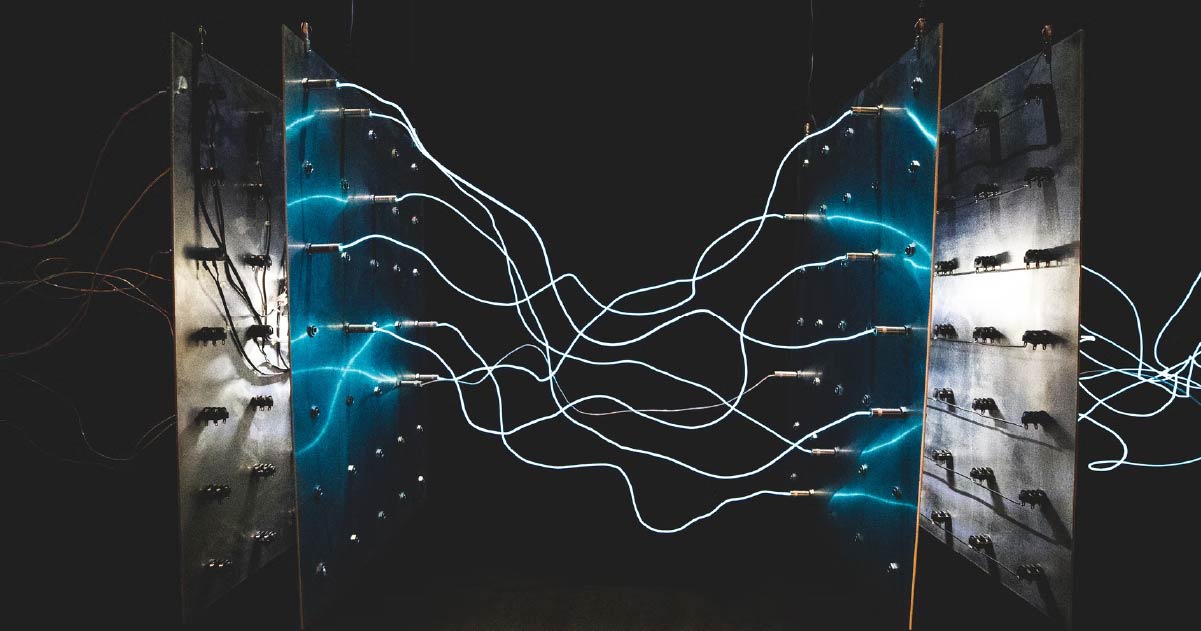
Energy
It is one of the necessary metals for the energy transition. It is used in solar panels, for example.
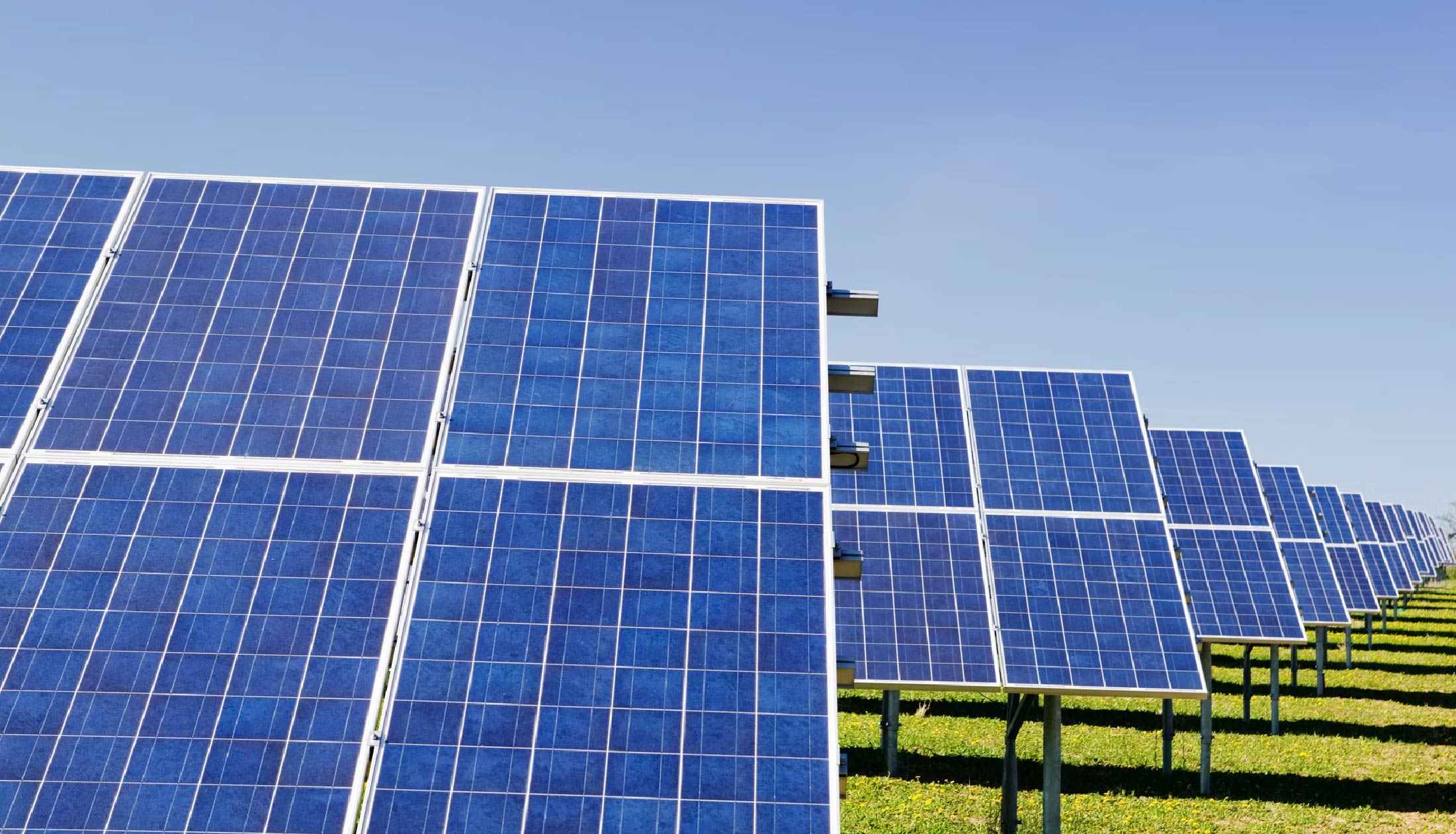
Food
Widely used in the coating of other metals to prevent corrosion such as tin-plated steel containers -cans-. Also in electrical structures, pewter, etc.
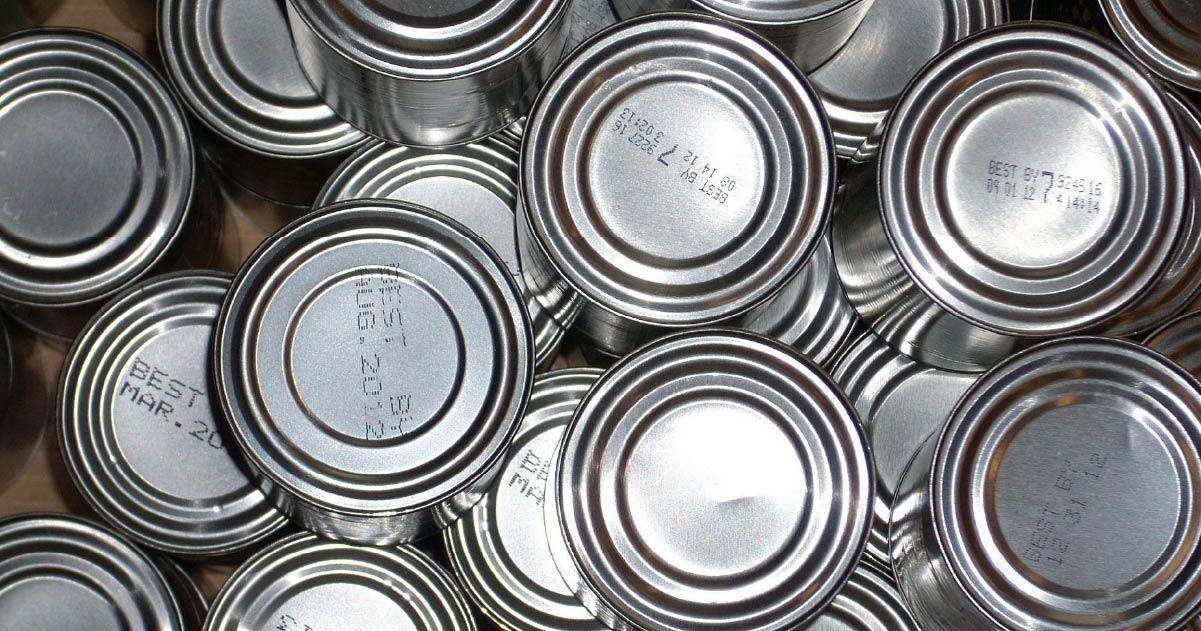
Medicine
Niobium-tin alloy is used for superconducting magnets, for MRI scanners, for example.
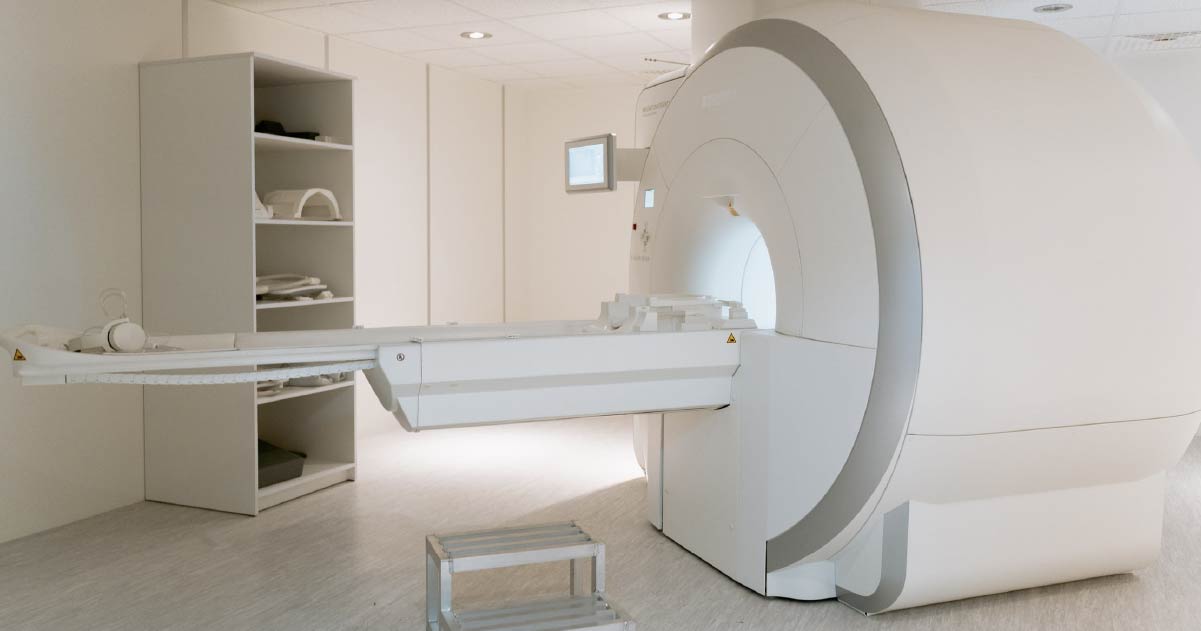
Dentistry
Tin fluoride is added to dental care products.
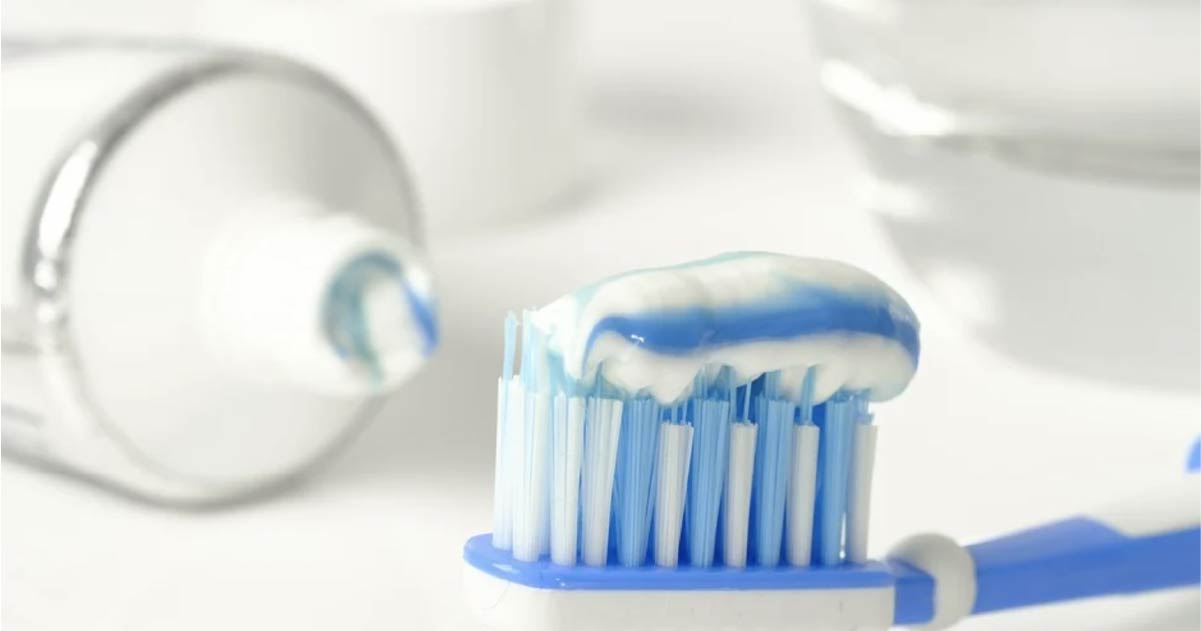
Aerospace
Used in alloy with titanium.
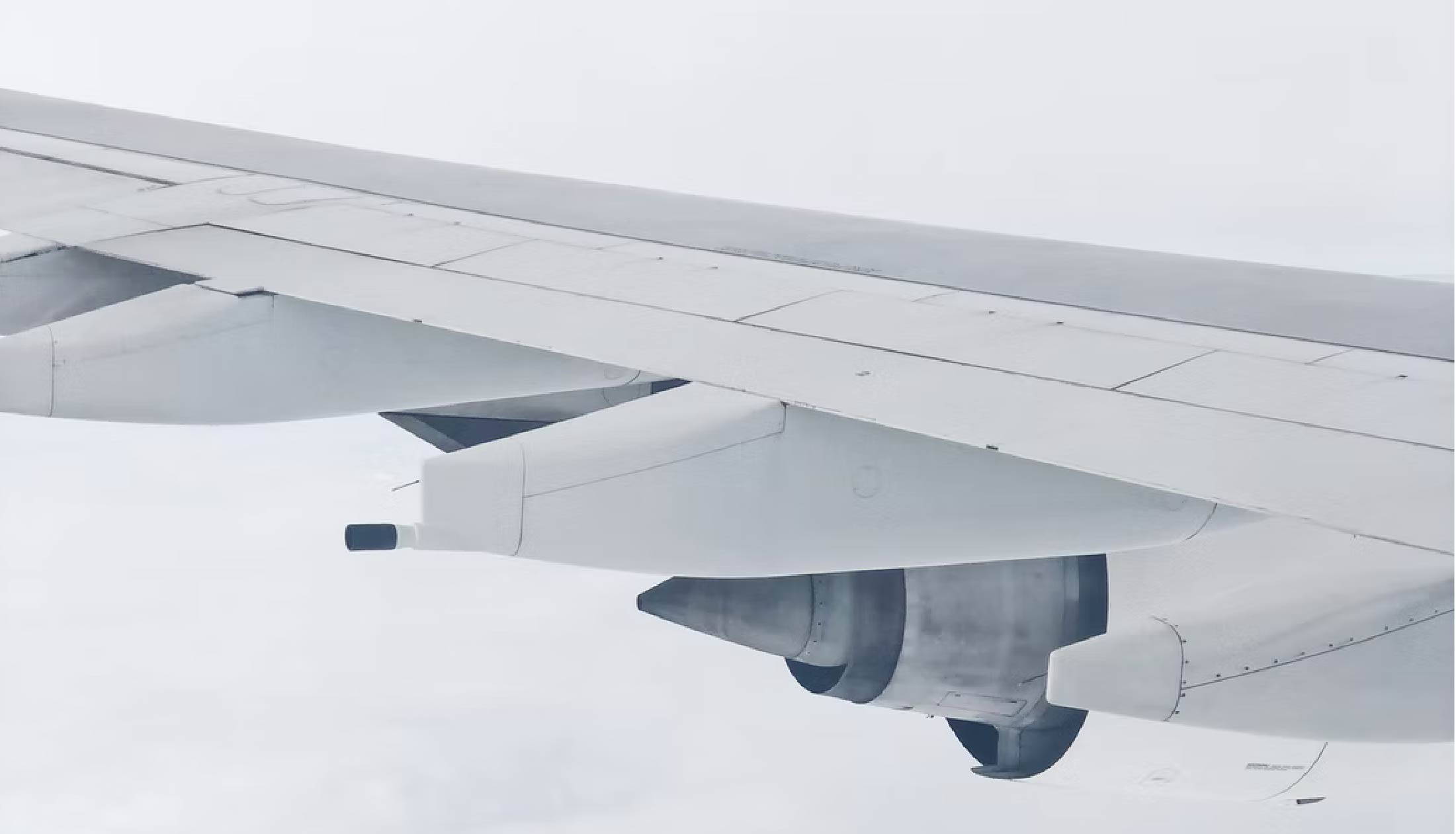
Winemaking
In the overcap on wine bottles, especially when the use of lead was banned for this purpose.
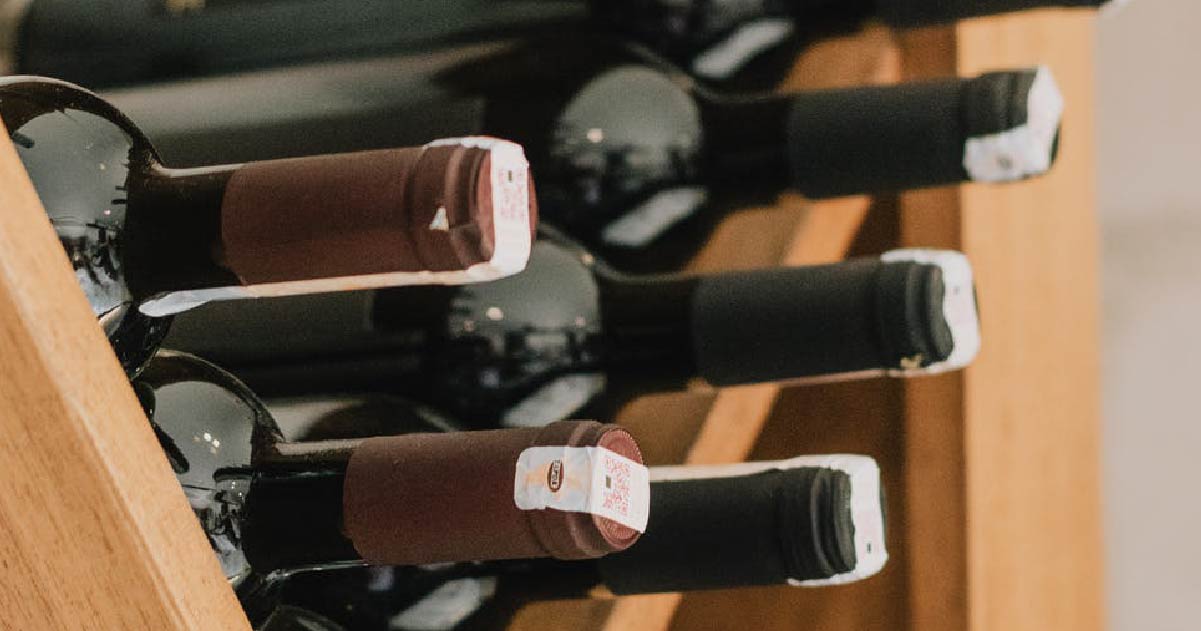
Glass
Molten glass is floated on molten tin to make a flat, flawless surface.
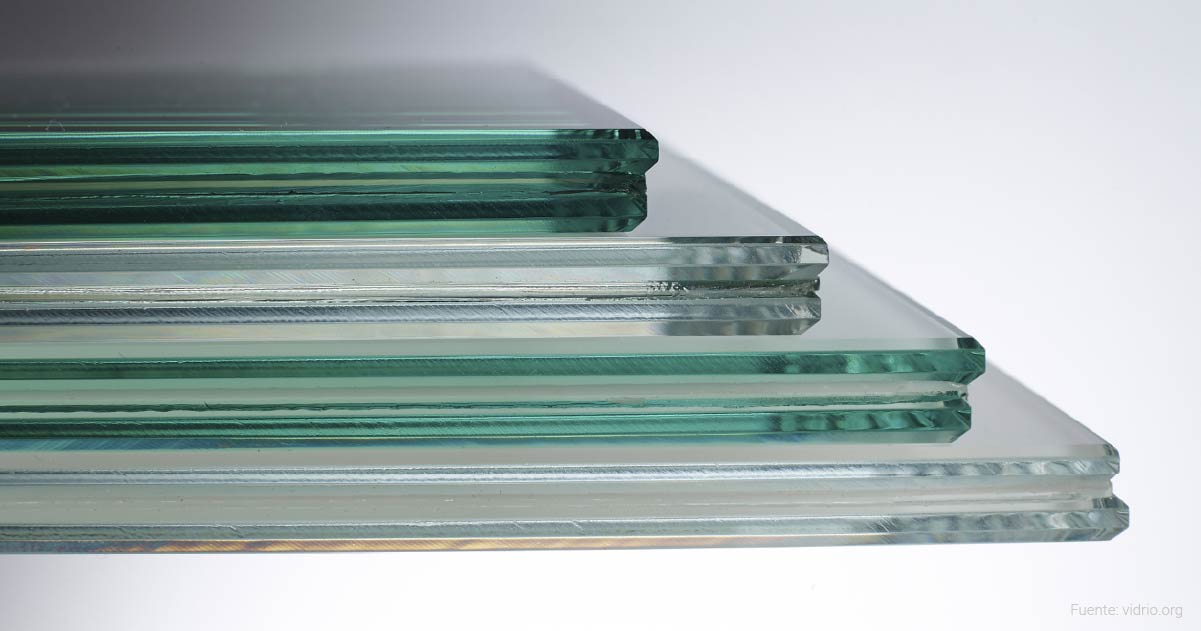
Soldering
It is a premium metal for soft soldering.
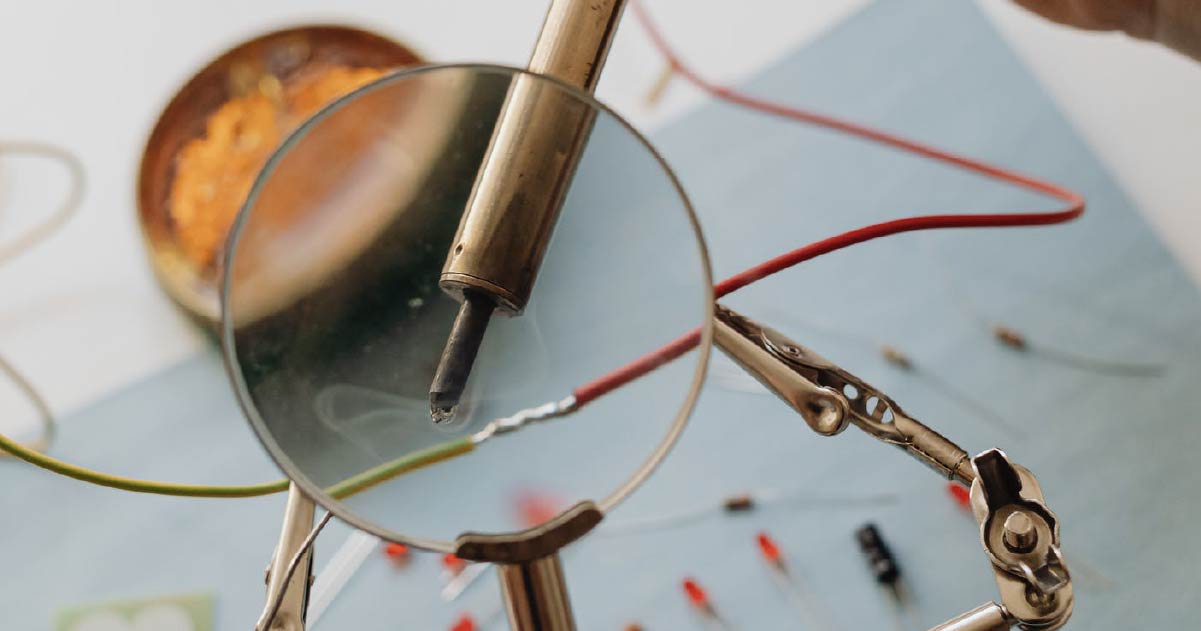
Lithium-ion batteries
Used as a negative electrode in advanced lithium-ion batteries.
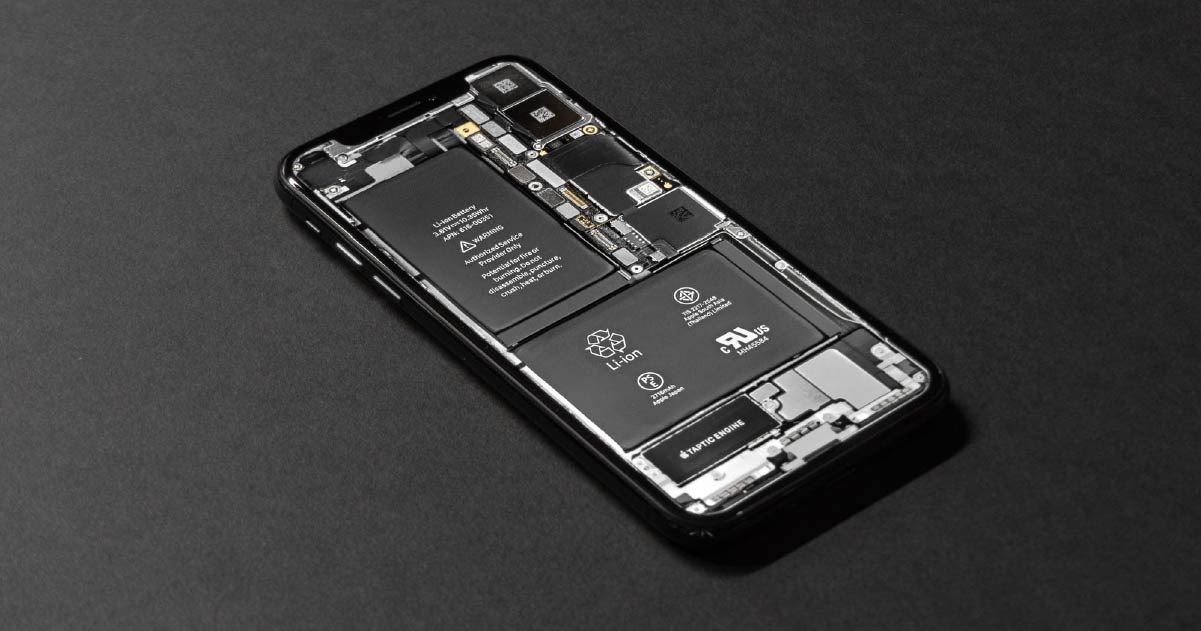
How is it obtained?
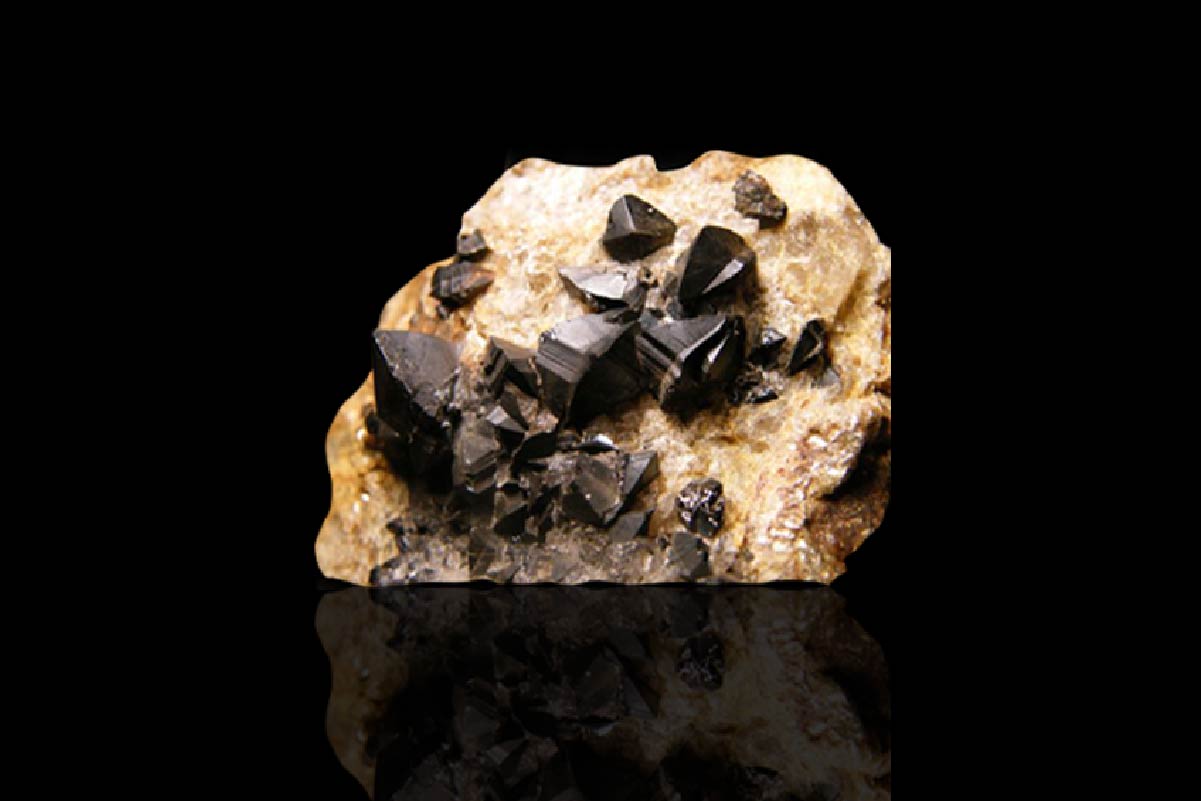
The process to convert cassiterite to metallic tin (Sn) is relatively simple. The mineral concentrates obtained by gravimetric and magnetic methods have to undergo controlled fusion (heating) processes, combining different variables, such as the heating temperature, the oxide-reduction conditions of the atmosphere and the use of different fluxes.
1
A grinding process is applied to reach the liberation size of the metal ores.
2
Gravimetric methods and water are used to achieve the separation by density to obtain the metallic mineral concentrate.
3
The concentrate obtained is subjected to an oxide reduction process by fusion to obtain the tin metal.
4
Optionally, to obtain 99.99% tin, it is subjected to an electrolytic process.